Dual mass flywheels (D.M.F.)
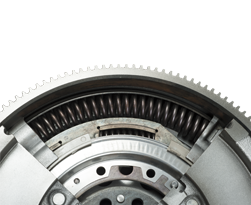
Dual mass flywheel for the best vehicle efficiency and driver comfort. Every second car which rolls off the assembly line is fitted with a DMF - this equipment rate is continuously increasing. The dual mass flywheel helps filter out dynamic vibrations between the engine and the gearbox. Thanks to two independent flywheels connected via a bearing or bushing, including a damper system, DMF proofs the sensitive gearbox and rest of vehicles against the engine explosions’ vibrations, thus improving driving comfort. Choose Valeo :
- Designed for long lasting performance > High-grade “best-in-class” spring wire used > Long-life ball bearings and bushings (no maintenance needed) > Added friction damping system design is stable for life
- Specifically designed for each vehicle application > Tuned with low stiffness for maximum noise reduction > Optimized filtering performance for “rattling” and “booming” issues > Applications from 200Nm up to 500Nm torque engines
- Improved driving comfort > Improved gear shift comfort and gearbox synchronizer durability by reduction of clutch disc inertia > Fuel consumption reduction is achieved by driving at lower speeds due to excellent noise reduction
Among its latest launches, Valeo provides applications such as Peugeot 308, Citroën C4, Opel Astra, Mercedes A-B-C-S Class Valeo proposes 3 innovative solutions: DMF with inner damper : At high engine speeds, the centrifugal load pushes the springs against the spring guides and creates friction. Due to this friction, the active number of coil springs is reduced, therefore, the effective spring stiffness is increased and filtering capacity is reduced. In the DMF with inner springs, small straight springs are integrated in the drive plate. Less sensitive to the centrifugal load, they are able to filter the vibrations.
For some extremely demanding applications and especially on rear wheel drive (RWD) vehicles, it is necessary to obtain an extremely low level of vibration at the gearbox entry level. Valeo’s long travel damper (LTD) technology, developed for automatic transmission damping, is integrated in the DMF to reach this target. Long travel damper DMF : The LTD DMF significantly reduces perceived vibrations and engine noise. This represents a major step forward in powertrain filtration technologies.
This advance is especially important as the fuel-saving engines now being developed have higher torque and, consequently, generate greater vibrations, particularly at low speeds. The LTD DMF absorbs torque vibrations generated by the engine to the transmission, thereby increasing the comfort of the vehicle's occupants. Two compact filtration devices give the LTD DMF the qualities required to become an essential component in tomorrow's conventional high-performance engines as well as for hybrid powertrains, which have the strictest installation constraints. The LTD technology is based on two sets of three springs operating in series and synchronised by a back plate. The straight springs are less sensitive to the centrifugal load than the curved springs. This provides less friction, hence the filtering is better than the one with curved springs.
In addition to the known dual mass flywheel technology, the LTD DMF integrates a long travel damper developed by Valeo for torque converters in automatic transmissions. This combination allows it to provide optimal filtration, especially during the startup, thanks to a maximum angular displacement of 80°, as well as an exceptional performance level in all engine regimes. Valeo’s long travel damper dual mass flywheel offers comfort levels which had never been achieved previously on the most fuel-efficient engines.
The NVH (Noise-Vibration-Harshness) level and ease of gear changes offer remarkable driving comfort for even the most vibration prone engines. Flexible Flywheel: The crankshaft bends under the force of the strong combustions inside the engine cylinders. This generates wobbling of the axis on the flywheel, which is bolted to the end of the crankshaft. Stress occurs between the bearings and the crankshaft, generating vibrations. If not filtered, the result is a roaring noise caused by the engine, a flywheel axial vibration and a potential increased vibration on the clutch pedal.
The flexible flywheel filters the axial vibrations transmitted through the engine crankshaft. This is achieved by adding a flexible plate at the engine side of the flywheel mass. The crankshaft deformation continues, but is not transmitted to the flywheel thanks to the flexible plate leading to reduced engine noise at high engine speeds, a reduced bending stress on crankshaft and a reduced level of vibration on the clutch pedal